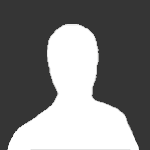
Пічка зі спіралей
Автор
makks,
27 повідомлень у цій темі
Створіть акаунт або увійдіть для коментування
Ви маєте бути користувачем, щоб залишити коментар
-
Зараз на сторінці 0 користувачів
Немає користувачів, які переглядають цю сторінку