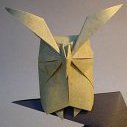
І щодо лімбів. Якщо вам треба швиденько зробити ділильний диск, в нагоді може стати ось цей онлайн калькулятор - https://www.blocklayer.com/circle-divider.aspx
- Детальніше...
-
- 1 коментар
- 1 393 перегляда
Блог користувача: Zalizovskiy
Залізне хоббі в запущеній формі.
І щодо лімбів. Якщо вам треба швиденько зробити ділильний диск, в нагоді може стати ось цей онлайн калькулятор - https://www.blocklayer.com/circle-divider.aspx
Пошліфував мені ДМ плитку, про яку я згадував раніш. Пошліфовано гарно як про мене. В будь-якому випадку, вона рівніша за все рівне, що у мене є в наявності.
Автор: Zalizovskiy,
Зварганив імпровізоване горно, назбирав алюмінієвого металолому і зробив своє перше алюмінієве литво. Після кількох спроб вдалося відлити цілком пристойні заготовки на ролики до гріндера.
Задоволений собою.
Автор: Zalizovskiy,
На поздовжній подачі мого токарного лімб був присутній з моменту його народження - фабричний.
А от на поперечці стирчав лише шмат шпильки та гайки. Це було вельми незручно. Якщо при "ловінні соток" я використовував стійку і індикатор і таки влучав в розмір, то при звичайних проходах користувався лише інтуїцією. Доходило до маразму - посадку під підшипник ловив, а при обдиранні міг пролетіти на пів міліметра. Довго так тривати не могло. Треба було або городити якийсь ПЦІ, або лімб. Ще коли починав ліпити докупи малого токарного вирішив, що при його створенні постараюся не використовувати мікроконтролери і сучасну електроніку (я сам електронщик по одній із професій), а обійдуся механікою і класичними рішеннями. Такий собі своєрідний відпочинок від сучасних технологій.
Отож зупинився на класичому рішенні. Стало питання заготовок. Про литво я вже писав. Після кількох днів експериментів я став власником кількох алюмінієвих відливок. Із одної з них я виточив нерухомий диск із вказівником:
Коментар щодо тимчасового - ота залізяка, яка прикриває гвинт поперечки планувалася як тимчасова. Скоро рік їй буде.
Тіло лімба і втулка:
Через втулку підтискається підшипник, вона сталева. Видно раковини на відливці - сховав їх на тильній стороні.
У втулці є проточка, в якій вставлено обрізок стрічки рулетки. То пружина така імпровізована.
Наступна проблема, яка виникла - створення ділильної приспособи для нанесення поділок.
Гвинт поперечки зроблено із будівельної шпильки діаметром 12мм і кроком 1,75мм. Не надто зручний крок. Прикинувши я вирішив ділити лімб на 35 поділок, через 5 соток. Шкала була надрукована на папері і наклеєна на фанерний диск діаметром 160мм.
Закріпив диск звичайним анкерним гвинтом:
Щоб зафіксувати патрон при нарізці міток нашвидкоруч зробив ось такий стопор:
В головці гвинта просвердлено отвір і туди запресовано латунну вставку, яку потім обточив.
Різець зробив із звичайного швидкорізу:
Як не дивно, такий сетап забезпечив цілком достатню точність. Я для перевірки пройшов два кола - мітки співпали ідеально.
Цифри набив китайськими 2мм штампами. Тут я поспішив, не став робити якусь приспособу для точного позиціонування штампів. Вийшло так собі, але хай це буде мотивом зробити краще.
Для перевірки спробував проточити щось орієнтуючись по лімбу. Після пари спроб вдалося легко досягти точності в 5 соток при проточці діаметра.
Висновок: лімб є зручною і потрібною штукою. Усім саморобникам рекомендую оснащувати свої творіння лімбами. При проектуванні верстатів намагайтеся використовувати гвинти із цілим кроком. У випадку готових базарних шпильок найбільш прийнятною є як про мене шпилька діаметром 18мм. Крок у неї 2мм.
Не робіть лімби малого діаметру. Якщо є можливість, намагайтеся зробити їх якмога більшими. Мій лімб має діаметр близько 50мм.
P.S. Накаточних роликів у мене ще немає.
Автор: Zalizovskiy,
Як часто трапляється, піч зробив із того, що під ногами валялося:
Так, без колісників, повітря просто вдувається збоку. В якості палива використовував деревне вугілля, що отримав після пересіювання попелу.
Результат:
Два пробних "млинці" та заготовки лімбу та ролика для гріндера.
Майже рік токарний вмикався банальним встромлянням вилки в розетку. Часто це було незручно, інколи - небезпечно.
І от, сподобився я зробити кнопочний пульт. Кнопки використав із вбудованим реле. Такі часто ставлять в бетономішалках. Штука зручна і практична. Корпус зробив із обрізка оцинкованого профілю.
Типовий спосіб виготовлення шківів в домашніх умовах (за виключеннями ДМ) - відливання із алюмінію заготовки і наступна токарка. Як варіант "зовсім нашвидкоруч" - точіння шківа із фанери. Якраз фанерний шків у мене зараз і працює. Він добряче підтерся і під навантаженням інколи підсмерджує паленим деревом. От я і почав задумуватися про заміну. Домашньої ливарні у мене поки ще немає (але буде, надіюся).
І от, під час подорожей по YouTube трапилося мені наступне відео:
Поміркувавши я дійшов думки, що подібне реально зробити і на моєму саморобному станку.
Звичайно, 4мм залізом мій "гном" вдавиться, а от 1.8-2мм думаю загне.
Отож до роботи. Роликом я вже хвалився. Виточив оправку:
...на яку надягнув шайбу, яка буде формувати профіль половинки шківа:
Центральний отвір заготовки діаметром 20мм вирізав коронкою. Вона має товщину 2мм і фіксується набором різнокаліберних шайб. Звичайно, такий спосіб кріплення лише перевірочний, треба буде виточити номальну шайбу для притискання.
Перший облом, який мене спіткав - різцетримач виявився нездатним надійно зафіксувати ролик. При боковому навантаженні він поступово сповзав і кут загинання кромки мінявся.
Викрутився я ось так:
Знову ж все на шайбах. Нормальна втулка для притискання в планах.
Після того, як зафейлив першу заготовку, наступних дві вийшли без проблем:
Нашвидкоруч зібрав шків на оправці - працює! Пасок щільно прилягає, не проковзує.
Проміжний результат позитивний!
Точити я хотів завжди.
Скільки себе пам'ятаю, завжди тягнуло до станків. Старався зрозуміти їх принцип роботи, особливості, характер, чи що. А особливо привертали увагу токарні.
Коли мені було років з 9-10 у нас перебудовували школу. Стару майстерню барахолили, переносили на інше місце. І я мав можливість на протязі кількох днів крутити ручки, як я тепер розумію ТВ-16. То була магія. Я мало що розумів, але точність станочної механіки добряче засіла в дитячих мізках. Пізніш, коли заходив до дядька чи товаришів на завод, я годинами спостерігав як засмальцьовані і часто напідпитку дядьки "давали план". Лунали слова "брак", "десяточка", "припуск", "лімб" і т.п. 1К62, за якими працювали дядьки були для мене якимись космічними агрегатами.
Але вперше за станок я став випадково. Мій колишній шкільний товариш закінчив ПТУ і в кінці 80-х розпочав трудову кар'єру. Працював він токарем, та ще й за модним тоді ЧПУ станком, здається болгарського виробництва. А у мене виникла потреба проточити якийсь валик. Звичайно ж я пішов до Вітьки. Він з радістю взявся за роботу і через десяток хвилин деталь була готова. Добре пам'ятаю, як світлодіодні цифри на УЦИ перетворювалися в реальні розміри моєї деталі. А потім товариша кудись позвали. Він півжартома кинув "- Ти тут експериментуй, я щас...". Я ж сприйняв фразу буквально. Швидко розібрався з маховичками, кнопки вмикання приводу патрона і переходу з програмного в ручний режим я запам'ятав раніше. Зараз я розумію, що швидкість обертання шпінделя була завеликою, але тоді я лише зачаровано дивився, як з-під різця виходила гарна рожева стружка, відразу завивалася і синіла в лотку під станком. Логічність керування і точність рухів захопили мене так, що я не зчувся, як спустив всю деталь в стружку. Це засмутило мене, адже я ніц не розумів, як вставити нову заготовку в патрон. З горя я почав обережно тикати кнопки на консолі. При переході в програмний режим станок сказав "Псс!!!", кулачки патрона розвелися, з його нутрощів виліз металевий циліндр, різець зобразив з нього якусь втулку, відрізав її і станок знов затих. "- Ага!" подумав я. Ще одне натискання кнопки на консолі, циліндр знов в патроні. Я швиденько давлю аварійний грибок і станок затихає. Перемикаю в ручний режим і насолоджуюся своєю владою над станком. Через пів години Вітька чухає потилицю і розмірковує над тим, як списати зпиляну мною в стружку заготовку довжиною щось зо три метри.
З того моменту пройшло багато часу. Але чарівне відчуття, яке відчуваєш коли заготовка стає деталлю не забулося.
Кілька разів я задумувався над покупкою власного токарного. Але тверезо прикинувши, приходив до висновку, що для моєї сім'ї то занадто. Грошей тих я точно не відіб'ю, а куди приткнути навіть10кгрн питання не виникало. Так-так, сімейство, господа, болячки та інша суєта.
Отож я трошки заспокоївся і прийшов до рішення, що якщо потрібен токарний, то або саморобний, або ніякий.
А моя новітня токарна історія почалася з оцієї теми:
Знайшов час на конструкцію вихідного дня.
Малий токарний, як не дивно, з самого народження був здатен відрізати. Обережно, невеликі діаметри, вузьким різцем але в нього це виходить.
Аж ось впарило мене відрізати заготовку 70мм діаметром.
Лол, кєк, мда...
Коротше, допилював я ту залізяку ножовкою. А по завершенню згадав, що існують в природі пружинні різці.
Порився в своєму підверстачному металоломі, трішки попрацював і зліпив наступну споруду:
Як видно, в якості ріжучої частини я використав обрізки циркулярного диску з твердосплавними напайками.
Товщина основної частини 12мм, отвір діаметром 10мм.
Спочатку сумнів викликав спосіб кріплення ріжучої частини (гвинтом із конічною головкою). Але після перших спроб конструкція довела свою життєздатність.
Пластина, яка затискається в різцетримач прикріплена до основної двома гвинтами, штифтом та ще й краплею зварки ззаду.
Ріжучу частину взяв із якогось китайського донора. Твердосплавна напайка виявилася дрібною і вельми твердою. Точилася вона досить неохоче. А малі габарити твердосплавної пластинки сприяли її вириванню при перекосі різця. Я плюнув і розкромсав старий бошівський диск. Твердосплавна частина там була немалих габаритів і точилася дуже схоже на ВК8.
Як результат вищеописаної діяльності я отримав можливість зовсім без проблем відрізати шайбу від кругляка діаметром 75мм.
Усіляко рекомендую описану конструкцію для повторення.
Автор: Zalizovskiy,
Трішки приакуратив станка, подороблював дрібниці на зразок короба для відводу стружки, поганяв на різноманітних дощечках. При наявному комплекті шківів на валу вийшло 4100 обертів в хвилину. Чистота обробки дозволила без проблем зібрати щити і їх же профугувати після склеювання.
Залишилася циркулярна частина і було вже почав прикидати що до чого. Аж "внєзапно", у таточка виникла потреба в свіжозбудованому станкові. Відмовити не можна - ледве завантажили втрьох творіння на причеп і поїхало воно у Київську область. Отож циркулярна частина стала на паузу.
Видно короб для відводу стружки і кришка клемної коробки двигуна. Знайшов таки. Ех, пофарбувати б...
Автор: Zalizovskiy,
Перед тим як ліпити докупи залізяки, непогано було б озвучити (навіть для самого себе) відповідь на запитання "Що мені треба від того токарного?".
Майже постійно мені були потрібні невеликі втулки, шайби, корпуси для невеликих підшипників (203 максимум), коліщатка, шківи, оправки. Крім того, вельми гостро стояло питання отворів великого діаметру (20-40мм) в відносно великих (150х40х80мм) деталях. Матеріали - пластик, дерево, кольорові метали, сталь. Тобто все, що під руку трапиться. Діаметри - навряд чи більше 80мм, шківи до 150мм. Досить часто виникала потреба торцувати чи проточувати довгий тонкий вал. От і все техзавдання.
З цього витікають вимоги:
Бюджет. Я розумів, що більша частина бюджету може піти на інструмент і вимірювальні прилади, тому орієнтувався на той, що був в наявності, або був відносно доступний. Для себе я визначив суму в 4000грн. Ця сума була для мене відносно підйомною без значного дискомфорту для сімейства.
Звичайно ж я розглядав варіант "підзбирати". Тобто збільшити бюджет вдвічі. За ці гроші були доступні розкомплектовані ТВ-16 в стані металолому, різноманітні варіації на тему ТН і уламки ТВ-хх незрозумілої комплектності. Звичайно ж, для їх відновлення потрібно було б ще "підзбирати". А мій бюджет+2*"підзбирати"=китайський настольний токарний.
Доступу до станочного парку я не маю.
Тому було прийнято рішення ліпити саморобного кадавра максимально використовуючи заводські вузли.
Першого "заводського вузла" знайшов любимий таточко, далася взнаки близькість місця проживання до природнього ареалу механізаторів:
Автор: Zalizovskiy,
В чіпмейкерській практиці часто виникає потреба швиденько поміряти частоту обертання якогось валу, шпінделя чи чогось подібного. Зазвичай, тахометра під рукою не трапляється. Спробуємо обійтися мультиметром, який може міряти частоту струму. Більшість популярних приладів це роблять. Для прикладу ось мій мультиметр, ввімкнений для вимірювання частоти:
В якості чутливого елементу нам буде потрібна якась котушка індуктивності із розімкненим магнітопроводом. Простими словами - шмат заліза з намотаним на нього мідним дротом. Найкраще підходить котушка звичайного автомобільного реле на 12В. Цілком підійде автомобільний ДПКВ чи щось подібне. У мене по гаражу вже років зо два валяються залишки жигулівського реле, його я й використав:
Чіпляємо виводи котушки до щупів мультиметра. Полярність ролі не грає.
У мене все це господарство виглядає ось так:
Ми будемо міряти частоту обертання свердлильного патрона. Придивившись, можна помітити, що я туди причепив невеликий магнітик.
Вмикаю свердлилку і підношу сердечник котушки реле до магнітика:
Відстань від котушки до магнітика самі бачите. На достатній відстані відчувається характерна пульсація, магніт починає притягувати сердечник.
Опа, мультиметр щось наміряв:
Далі рахуємо. Ми отримали приблизну частоту коливань в 14Гц. 1Гц це одне коливання в секунду. Значить, магнітик 14 разів за секунду проходить коло сердечника. В хвилину він це робить 14*60=840. Маємо частоту обертання патрона свердлилки 840 обертів за хвилину.
Автор: Zalizovskiy,
Дружина зварила борщ, спекли м'ясо в духовці, відлив заготовку (тигель поставив прямо в грубку) та ще й в хаті натопив!
Автор: Zalizovskiy,
Ще в часи царя Гороха купив я невелике китайське точильце. Навіть на момент покупки стан у нього був "не ахті". Після вмикання, точило починало гуляти по столу, підскакуючи і вібруючи.Так як використовував я його для обдирки ржавих залізяк і гостріння сокири, мене то влаштовувало. Особливо, після того, як притягнув двома гвинтами до важелезного верстака. Точильце і тут проявляло свій норов: при вмиканні і вимиканні на секунду-другу точило і верстак зливалися в резонансі і з останнього щось обов'язково падало додолу. Так тривало досить довго, до моменту, коли я зробив свердлильну стійку і виникла потреба точити свердла. В оригінальному стані робити цю процедуру на точильці було не надто комфортно. Крім того, зашелестіли обидва підшипники.
Коротше, я його розібрав. Поприколювався над якорем розміром з невелике яблучко, зацінив литий корпус товщиною з міліметр. А потім звернув свою увагу на вал. З правого боку він був відносно адекватним. А от з лівого, як посадка круга, так і зацентровка на торці були зміщені по радіусу на добрих пів міліметра. Діаметр валу - близько 15мм. Я сказав "Гм" і пішов на базар. Там купив свіжий 200мм "білий" круг, оправку під нього на вал 14мм. Взяв в руки болгарку. З лівого боку вал відрізав врівень з підшипником. Праву частину вкоротив і підшліфував на ходу до діаметра 14мм. Перед цим, звичайно, поміняв підшипники. Діаметр валу я звичайно провтикав, як і циліндричність. Ще трохи вкоротив, ще трохи розшліфував. Після якоїсь ітерації оправка сіла на вал відносно рівно. Посадив круг, заправив його. Пошукав взаємне розташування оправки, валу і круга. З якогось разу знайшов положення, при якому точильце навіть не будучи закріпленим стояло на столі як вкопане. То була перемога.
Зробив заглушку на ліву сторону, щоб прикрити пеньок валу. Розширив захист, зробив станинку із шматка полички, гумові ніжки. Завершив діяння регульованим підручником. Точильце стало виглядати ось так:
Ось тут видно щойно імплантовану оправку:
Після усіх цих процедур точильце змогло адекватно заточувати свердла та інші металоріжучі приблуди. І робить це понині.
Саморобна розточна головка дала першу продукцію.
Працював на обертах близько 300об/хв.
Мінімальний діаметр розточки - 12мм, максимальний - близько 48, пробував лише 35мм. Отвори в деталі на фото мають діаметр 22мм.
Зловити п'ять соток можна без особливих проблем. Максимальний зйом - близько 1мм на радіус. Комфортний - 0,3-0,6мм. Це при вильоті твердосплавної частини близько 30мм. При зйомі 0,2мм і більше виходить красива вита стружка відрізками десь по 80мм. Чистота поверхні не ідеальна, але мене цілком влаштовує. На фото видно.
Опора кардану, про котру я вже згадував тут була проточена і виконувала роль шліфувального. Для цього я зробив фанерну планшайбу діаметром приблизно 300мм і обклеїв її шліфувальним папером. Приводилася в рух та машинерія від двигуна пральної машинки.
Навесні цього року в барахолці я купив малу поздовжну від 1Е61М. У цього станка їх було дві на вибір - класичної компоновки і з швидким відводом різця. От останню я й купив. Розрахунок був такий: поздовжнє переміщення різця буду здійснювати звичайним способом, а поперечкою буде механізм швидкого відводу різця. Штатний (поздовжний) хід складає 140мм, по факту ~150мм, поперечний я надіявся отримати щось близько 100мм (ширина малої поздовжної 140мм). Передньою бабкою буде вищезгадана опора кардану, станиною... ммм... станину зліплю з чого прийдеться.
Чим прийдеться виявився 160 швелер. Із нього була зварена ось така конструкція:
Розміри видно які. Конструкція була відпалена, вірніш "зістарена". З кольору мінливості видно до якої температури я її грів. Час витримки - дві доби.
А потім болгарка і "плоскошліф". Човгав я її кілька вечорів, але добився перепаду по площині близько 5 соток. Лише в кількох місцях залишилися ями до 0,15мм.
А потім знов взяв в руки болгарку, дриль і інші низькотехнологічні інструменти. І вийшло ось так:
Знов "плоскошліф", дремель, наждачка, імпровізовані шабери і т.п.
Накладка з круговим вирізом крім гвинтів посаджена ще й на епоксидку.
Усі ці жертви для того, щоб вийшло ось так:
Так зробив привід поперечки:
Прикидаю компоновку:
В якості ходового гвинта використав шпильку М12. Гайка - саморобна, капролонова. Закріплена ось так:
Проєм перед нею вибраний в чавуні - місце для підшипників і піджимних гайок. "Фрезерував" дремелем (гравером).
Чесно кажучи, дивлячись на якість виготовлення малої поздовжної турбувався про те, щоб напрямок руху поперечки був строго перпендикулярний поздовжному, але обійшлося.
Швиденько виготовив різцетримач:
Із товщиною матеріалу стався деякий оверкіл - 20мм. Але що було - то було. Зато не погнеться. І таки так, подібний "оверкіл" трапиться не один.
Завершив апокаліптичну картину стіл, куди я присандалив станину майбутнього токарного. Я того стола зробив раніше із дубових віконних луток.
Стіл мав фатальний недолік, який відразу став його перевагою - він був важелезний. І рівний.
Із шматка фанери, обрізків металопрокату і жигулівських запчастин на швидку руку був виготовлений кронштейн двигуна:
В процесі виготовлення підкладки під корпус передньої бабки (так, опору кардана вже перехрестили!) закономірно дав в штангу, що для мене характерно.
Дремель в руки і гайда:
Товщина 28мм. Не зважаючи на непристойний вигляд, після "плоскошліфа" підкладка дотепно "плавала" на станині від легкого доторку. А після притискання відривалася з помітним зусиллям. Так само поводив себе і корпус передньої бабки. Особливо цікаво було обертати підкладку в один бік, а корпус бабки в інший. Рухалися як на підшипниках.
Все було готово до запуску.
Автор: Zalizovskiy,
Зібравшись із силами і назбиравши металолому я взявся за фуганок.
Після кількох днів міркування і роботи болгаркою та зваркою народилася ось така конструкція:
Двигун там просто для примірки.
Швелери зварені між собою трьома відрізками труб. На краях діаметр труб 108мм, посередині - 82мм.
З іншого ракурса:
Площину під корпусами опор валу вивів "шабрінням болгаркою". Станину варив точками, даючи металу охолонути. На щастя конструкцію не покрутило.
Для "столів" зварив каркаси із прямокутної труби:
Площина їх виводилася на "плоскошліфі" - шматку товстого ДСП накритого шліфувальною шкуркою 400х1100мм. Потім свердлилися отвори і гвинтами М6 з потайною головкою пластини кріпилися до каркасів.
Все це суттєво додало їм жорсткості.
Опісля, зібрані столи ще раз шліфувалися на "плоскошліфі".
Регулювання висоти прийомного столу, видає в мені жигуліста зі стажем:
А от схема регулювання висоти подаючого столу попила мені крові. Я тижнями крутив в голову різноманітні схеми. На ексцентрики не було грошей, як і на направляючі. Конструкції де стіл тримається на важелях, які нахиляються я відмів як не жорсткі. В результаті народилася наступна схема.
Із квадратної труби 30х30 зварив дві рамки шириною строго як ширина між швелерами станини:
Нижня, нерухома рамка прикручена до станини:
Між собою, як видно, рамки стягнені двома 16мм гвинтами+широкі шайби+пружини клапанів того ж жигуля.
Кут нахилу площини рамок до площини столів - близько 30 градусів. Звичайно ж площини рамок виведені на "плоскошліфі".
До верхньої рамки приварив ось таку конструкцію:
Два наварених кутика утворили горизонтальний майданчик для подаючого стола.
На головки гвинтів, які стягують рамки наварив довгі гайки, через які пропустив 12мм шпильку:
Обертаючи шпильку можна рухати верхню рамку під кутом до площини столів, а з нею і подаючий стіл.
Конструкція вийшла проста і доступна. Річна експлуатація показала її життєздатність.
Далі буде електрика і перша стружка.
P.S.Відразу вибачаюся за якість фото, на той час під рукою був лише BlackBerry Bold.
Автор: Zalizovskiy,
Із двигуном мого фуганку трапилася стандартна історія. Без таблички, без будь-яких опізнавальних знаків, повний тирси, передній підшипник закоксований всмерть. Підшипник я швиденько замінив, тирсу вичистив, обдер і за допомогою старшого пофарбував. Стало питання визначення потужності і підключення.
Прийшлося застосувати дедуктивний метод. Діаметр валу - 28мм. Відстань між отворами на лапах - 110мм. Зі слів таточка: "- Мужики сказали, що три кіловати".
Обмотки з'єднані зіркою. Спершу роз'єднав обмотки і повиводив їх початки. Чисто для експерименту. Спробував запускати з конденсаторами. Виходячи з "трьохкіловатності" потрібно було 210Мф. Необхідної ємності у мене в наявності не було, отож прийшлося шукати та замовляти. І от, із Маріуполя приїхав МБГВ 200мф 1000В. Движок приємно і м'яко стартував із вказаним конденсатором при вмиканні зіркою і працював без робочого конденсатора взагалі. Дивно. В трикутнику із підключеним конденсатором трошки перегрівався, значить 200мФ для нього занадто (для 3кВт двигуна треба 210мФ). Але це точно не 2,5кВт двигун (у них вал 22-25мм діаметром). Одним словом, так і залишив. Для пуску підключав конденсатор, працював без нього.
Із бляхи зігнув коробку і розташував в одному із швелерів станини:
Дерев'яна коробка коло двигуна містить конденсатор.
Бонусом новий шків (привіт барахолці Чіпмейкера!) і регулятор натягу ременя:
Автор: Zalizovskiy,
Мітчика я переміг. Ціною роздовбаної шліцової. Але постраждала вона лише естетично. Міцність тої досить дебелої залізяки не була порушена.
Зібрав те господарство: спочатку залишки шліцової, на неї лягає заготовка планшайби, яка одночасно сідає на циліндричну посадку шпінделя. Знову шпилькою все це господарство стискаю шпилькою, затягую гвинти в отворах, де щойно нарізав різь і приварюю шліцову до заготовки планшайби. Так як навантаження на зварку буде невелике, фактично лише частина обертального моменту, то роблю три відрізки шва по півтора сантиметри довжиною. Варити незручно, оперую фактично в щілині шириною трохи більше 10мм. Але я справився.
Ще один момент. Заготовку планшайби спеціально брав із низьковуглецевої сталі, щоб не загартувалася при зварці.
Викручую вже непотрібну шпильку і починаю дерти:
Кути заготовки трохи зрізав болгаркою. Це полегшило роботу, але все одно для станочка процес став випробуванням. Яке він з честю витримав.
Заготовка з-під газорізу, мала кілька твердих включень, які майже відразу скололи пластинку на різці. Перевернув її і продовжив роботу.
Поступово почали проявлятися контури планшайби:
Відео процесу:
Ще трошки роботи і маю гарненьку планшайбу, на яку щільно, але від руки сідає патрон:
Розмічаю і свердлю отвори, прикручую патрон і маю:
Пізня ніч, стомився ледь з ніг не падаю. Але не втримався, затиснув якийсь обрізок труби, проточив. Точить!
Автор: Zalizovskiy,
Замінив у дерев'яному точилі оцупок круга на нормальний 200мм круг шириною 25мм. Ширини захисту, як і очікувалося не вистачило, отож прийшлося робити нову, бляшану полосу, яка задає відстань між боковими панелями. Я так робив у точильці, після заміни оправки. Нова, ширша бляшка вже вирізана і пофарбована - сохне. Фото результату завтра.
Стартує точило помітно важче, але потужності вистачає з немалим запасом. Точити різці таким кругом - одне задоволення.
Автор: Zalizovskiy,
Щоб закріпити патрон на шпінделі, необхідно до чогось причепити планшайбу. Звичайно, кортіло просто приварити на кінець валу шмат заліза і проточити його. Але тоді передня бабка фактично стає нерозбірною, якщо витягти вал з підшипниками з корпусу теоретично ще можна, то зняти передній підшипник і його кришку - ніяк. Тому це не наш метод. Вирішив використати шліцову частину фланця кардану, який в мене був. Планшайба буде зафіксована від радіального переміщення тугою посадкою на циліндричну частину шпінделя (яку треба проточити), а від провертання будуть страхувати шліци, які будуть піджиматися додатково гвинтами. Крім того, шліцова частина буде впиратися у внутрішню обойму переднього підшипника, додатково посилюючи усю конструкцію.
Не полінувався, виставив співвісність супорта і бабки. Базувався по корпусу бабки, площина прилягання передньої кришки пласка і рівна.
Отож, спочатку проточую циліндричну посадку для планшайби:
Вибачайте за якість, фотографував на упаковку від жигулівського масляного фільтра.
Видно картонний пильник, це я так пожалів передній підшипник.
Далі одягаю на залишки шліців фланець, притискаю його шпилькою крізь прохідний отвір шпінделя. Торцюю:
До фланця притискаю і прихвачую зваркою по кутках заготовку майбутньої планшайби:
Розточую в заготовці отвір по діаметру циліндричної частини, яку я проточив раніш.
Для вас це все звучить банально, але я тоді наче на Місяць висаджувався: вперше працюю розточним різцем, вперше переточую різці для своїх потреб, ломаю їх, знов переточую.
Проточив, розібрав те господарство, відрізав наварену заготовку.
Болгаркою відрізав шліцову частину від фланця і обточив її:
У мене з'явилися дві бази для планшайби.
На циліндричну частину тугенько саджу заготовку планшайби, додатково притискаю її шпилькою і торцюю:
Потім свердлю отвори в шліцовій частині, щоб затиснути її на шліцах. Нарізаю там різь М6 і ...вриваю мітчик. Наступних три години я його звідти виколупую.
"Врятував від мартена" (с) плитку 250х250мм.
Стан цілком пристойний. Гвіздки на ній не рівняли, посередині симетрична яма до десятки. Скоріш за все віддам на шліфовку. Шабрити немає по чому, а на "три плити" у мене не вистачить ні терпіння, ні часу.
Добре бути любителем без досвіду. Будь-яка практика і нові вміння викликають відчуття власної значимості і всемогутності.
Давно не працював за токарним - то ремонт, то робота. А от на цих вихідних потокарив донесхочу.
Вирішив випробувати одну штуку, про яку розкажу пізніш. А для цієї штуки потрібен ролик, який можна затиснути в різцетримач. От і взявся за роботу. В якості ролика використав підшипник, рішення очевидне.
Точу вісь ролика:
Заготовка - шток від амортизатора.
Свердлю.
Ріжу різь.
Зібрав. Сіло щільно, посадки я вже навчився робити.
Фрезерую площину.
Одне із застосувань показав у відео:
Автор: Zalizovskiy,
Після того, як патрон став на своє місце, залишилося доробити ще одну дрібницю. У бабці позаду, між шківом і заднім підшипником світилася чимала діромеха. Штатно там повинна бути шліцова частина другого фланця. Якого у мене не було. Але у мене залишилися обрізки того, з якого я робив планшайбу. І в мене проскочила думка "- А може спробую її порізати?". Видобув із своїх запасів брусочок рапіду, заточив його як умів, зобразивши відрізний різець. Вийшло так собі, але за кілька спроб я підібрав більш-менш вдалі кути.
Залишок фланця взяв на розжим, за кромку 4-5мм шириною. Акуратно, помаленьку, попердюючи, але станочок різав!
Не сколупував голочки, а давав нормальну стружку. Діаметр фланця в тому місці становив десь з 70мм, метал був трошки прикалений, що ускладнювало задачу. Подавав я помаленьку, але фланець в кінці-кінців здався.
Я обнаглів, запхав в патрон якийсь шмат кривезної труби і спробував різати його. Не те щоб ідеально, але я його відрізав.
Я не очікував, що моя саморобка от так відразу буде хоч якось різати досить незручні заготовки. Це було вельми мотивуюче. Відразу згадалася цитата: "Для вузла кардана то непринципово, але це зменшить допустиме радіальне навантаження та жорсткість Вашого вузла. Пластик точити і то легенько." звідси
Обрізок труби я трохи розточив зсередини, обрізок шліців трохи підторцював отримавши такі супердеталі:
Обрізок труби став своєрідною дистанційною втулкою, одним боком вперся у внутрішню обойму заднього підшипника, за ним стала шліцова шайба. Її підтиснув шків.
Діромегу вдалося затулити.
Ви повинні прийняти Умови використання.